链式输送机的张紧装置
链式输送机的张紧装置
电话:18803739170 发布时间:2019-12-02 11:31 本文地址:/baike/336.html
链式输送机以链条作为承载和牵引构件完成物料的输送工作。链条属于挠性牵引构件,其特点是承载能力强,承受载荷时伸长量小;能够绕过直径较小的链轮、导轮、滑轮及尾轮;能够十分方便地在其上固定各种输送元件。它与另一类挠性牵引构件———输送带一样,都需要有张紧调节装置,否则输送机无法正常工作。因此,张紧装置是链式输送机不可缺少的重要组成部分。其通常设置在输送机的尾部,可与尾轮一起实现同时调节。
1 张紧装置的作用
(1)链条装入输送机后,在未被张紧的情况下是松弛的,无法正常工作,只有使其获得一定的预张紧力(即初张力),才能使输送机正常运行。
(2)通常输送机的尾轮都是被动轮,靠与链条之间的摩擦力使其旋转。只有通过张紧装置才能使牵引构件与尾轮之间产生足够大的摩擦力带动尾轮转动,这对于光轮面及带槽光轮面的尾轮尤为重要。
(3)链条节距因磨损而逐渐变大,链条会逐渐伸长,张紧装置可补偿由此带来的伸长量,保持牵引构件的正常工作状态。
(4)牵引构件在适当张紧的情况下,才可减小悬垂度,减少与壳体之间的摩擦。也有利于链条与头轮的啮合及脱链。
(5)具有一定自动张紧作用的张紧装置,能对牵引构件因张力变化而引起的微小伸长或缩短进行随机的自动调节,可起到均载的作用。
(6)张紧装置是安装和拆卸所必须的,牵引构件是在未张紧的情况下装入输送机,装入后,可以通过张紧装置检查链条长度是否合适,是否需要增减;拆卸牵引构件时,应将张紧装置完全放松,否则拆卸工作将很难进行。
2 张紧装置的种类、特点及适用范围
链式输送机的张紧装置有螺杆式、弹簧螺杆式、重锤小车式、液压式4种。其中液压式很少使用,本文主要介绍应用较多的前3种张紧装置。
2.1 螺杆式张紧装置
见图1,在尾部2侧各配备1对螺杆、螺母,采用T型螺纹,人工旋转螺杆实现张紧调节。它有2种运动方式:一种是螺母固定,螺杆旋转并前后移动;另一种是螺杆只旋转不移动,螺母前后移动实现调节功能。按螺杆的受力方向,第一种方式又有螺杆受压或受拉2种形式。目前,我国链式输送机的螺杆式张紧装置以螺杆受压式的居多。
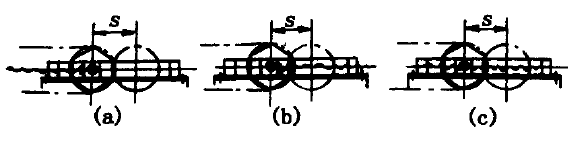
(a)螺杆受压式 (b)螺杆受拉式 (c)螺母移动式
螺杆式张紧装置的优点是外形尺寸小,结构简单、紧凑,调节比较方便、可靠。缺点是偶尔过载时,没有自动调节功能;张紧时尾部2侧的螺杆需分别进行操作,较难保持同步运行,必须在2侧交替拧动螺杆,且每次的调节量要加以控制方能保证同步。此外,由于输送机的牵引构件的张力在运行中不是恒定不变的,随着链条的磨损,其长度会逐渐伸长,因此需定期进行检查和调整,若调节不当,可能会出现"过张紧"或"过放松"的现象。尽管如此,这种形式的张紧装置仍然得到了比较广泛的应用。
螺杆式张紧装置主要适用于输送距离不长、载荷不大、速度不高、物料温度为常温的各种链式输送机。图1c所示的螺母移动式用于尾部位置狭小,螺杆移动不便,调节行程较大的情况。图1a和b可根据需要任选,其中螺杆受拉式的性能优于螺杆受压式的,因其螺杆头部伸出在尾部末端之外,设计中只需加上1对链轮和1根链条,便可方便地实现同步调节(拧动其中1根螺杆,2侧螺杆可同时移动,保证同步)。通常,选用螺杆受拉式较多。
2.2 弹簧螺杆式张紧装置
在图1a所示的螺杆受压式张紧装置中加入1个压缩弹簧,便构成了弹簧螺杆式张紧装置(见图2)。
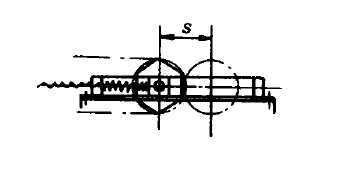
压缩弹簧应在尾轮轴承座与螺杆之间,即螺杆不直接与轴承座连接,而是在中间加进1个弹簧。拧动螺杆时,通过弹簧将作用力传到尾轮轴承座上带动尾轮移动。在此,螺杆是粗调,弹簧是微调整,固定螺母的位置和作用与螺杆式张紧装置相同。因受结构限制,其他形式的螺杆式张紧装置不能设计成弹簧螺杆式。
弹簧螺杆式张紧装置的优点是可实现一定范围内的微调,由于弹簧的弹性,在牵引构件的张力发生变化时,弹簧或拉伸、或压缩,可使牵引构件始终处在一种合理的张紧状态,这一功能是螺杆式张紧装置无法实现的。在链式输送机的运行中,受载荷不均等各种条件的影响,牵引构件的张力发生一定变化的情况经常发生,与螺杆式相比,弹簧螺杆式张紧装置更能适应输送机的这种工作状态,因而更加合理。其缺点是结构较复杂,弹簧的选择必须合理,刚性太大或太小均不能起到应有的作用;由于加入了1个较大的弹簧,会使尾部长度增加,重量也随之加大。
这种形式的张紧装置主要适用于输送距离较长、载荷较大、速度中速以上、物料温度高于常温的场合。工作中牵引构件的张力会随着工况改变或偶然因素发生一些变化,需要张紧装置对此作出随机反应,张力增加时,弹簧略压缩,使行程减小;张力减少时,弹簧略伸长,使行程加大,以确保链条与尾轮之间始终有足够大的摩擦力,保证输送机的正常工作。弹簧螺杆式张紧装置能较好地实现这种功能,而单纯螺杆式则无法满足这一要求。使用螺杆式张紧装置的地方均可用弹簧螺杆式张紧装置来取代,但反之则不行,这一点在设计和应用中要注意。
2.3 小车重锤式
小车重锤式张紧装置是将输送机尾部的尾轮轴系安装在1个装有4个轮子的小车上,每侧2个轮子和1条轨道,轮子可在轨道上滑动,将钢丝绳系在小车上,然后绕过滑轮,另一端挂有重锤,通过重锤的重量自动将尾轮张紧(见图3)。该张紧装置有2种形式:一种是地上式,有2个滑轮,重锤安排在地上;另一种是地下式,仅1个滑轮,重锤悬垂在地下。重锤应做成若干块,每块重量不宜过大,以便于根据张力的变化增减。
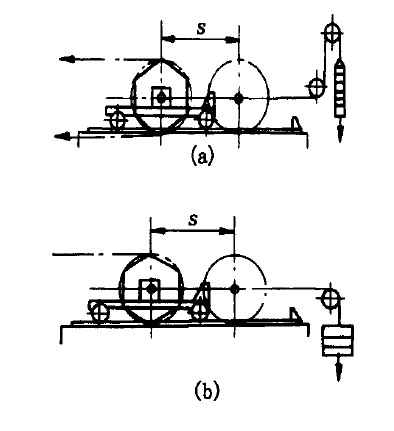
这种张紧装置的最大好处是变刚性张紧为柔性张紧,它能保证张力的恒定,可自动补偿由于温度变化、链条的伸长及链条磨损带来的牵引构件长度的变化,同时还能在偶然过载时降低链条的尖峰负荷值。其操作简单,只要调整好重锤的重量,便几乎不需人工操作,省去了上面2种张紧装置需经常要人工调节的麻烦。缺点是机构较庞大,结构较复杂,2侧需设轨道,占据的空间较大。
小车重锤式张紧装置主要应用于输送距离长、载荷大、链速高、张紧行程较大、引起牵引构件张力变化的因素较多的情况,特别适用于输送温度较高的物料。由于物料温度高、变化大,链条受热胀冷缩的影响,长度的改变量较大且无规律,张紧装置必须具有自动张紧和放松的功能才能适应这种要求。若尾部可设置在地坑里,应选用图3b所示的地下式;反之则选用图3a所示的地上式,但要比前者多用1个(有时是2个)改向轮。与前2种张紧装置相比,虽然这种形式的优点更多,但因其结构较复杂,造价高,占地大,故使用相对较少。
3 张紧装置的设计要点
设计张紧装置时,除了根据输送特性和工况条件正确选择其类型外,还需注意以下问题。
3.1 张紧行程的确定
张紧行程的大小根据链条节距确定,它与机槽规格、物料种类、输送速度及张力大小均无关。链式输送机使用的链条主要有模锻链、双板链和套筒滚子链3大类,前2种链条每次只可加入或卸下1个链节,张紧行程可取得较小;而套筒滚子链条每次需加入或卸下1对链节,相当于2倍节距,张紧行程应取得较大。计算张紧行程的经验公式为
S=(0.7~0.75)t·····························(1)
S=(1.25~1.6)t····························(2)
S=2t···························(3)
式中
S———张紧行程,mm
t———链条节距,mm
式(1)用于模锻链和双板链条,式(2)用于套筒滚子链条,式(3)是最大张紧行程的取值范围,仅用于长距离输送机或物料温度很高时。由于链式输送机所使用的链条是可以变化的,故通常都按式(2)决定张紧行程,其对上述3类链条均适用。推荐的张紧行程值见表1。
对于弹簧螺杆式张紧装置,还应考虑弹簧的长度和工作行程,一般是在张紧行程中加入弹簧的工作行程。为了不使尾部尺寸过大,S的最大取值不应超过2t。
3.2 初张力的选择
链式输送机必须有一定的初张力才能正常工作。初张力的作用主要是:(1)保证牵引构件与尾轮之间产生足够大的、能使尾轮转动的摩擦力;(2)依靠链条初张力,确定用于输送物料的刮板或附件的稳定位置。此外,在牵引构件的张力计算中,也要考虑初张力的因素。
初张力的大小应根据输送机种类及载荷性质确定。如对刮板输送机,初张力为3000~10000N;对埋刮板输送机,初张力为500~2000N。输送距离长、载荷大时取大值,反之取小值。在张力计算中,对较大的初张力应预计算,反之则可忽略。
初张力实质上就是保持运行的最小张力,此值过大会加快部件磨损,加大运行阻力;过小则牵引构件与尾轮打滑或牵引件挠曲,无法正常工作。所以正确选择初张力是很重要的。实际使用中,并不需要对初张力进行测试,也无法进行测试,只需利用张紧装置调节几个回合,使输送机空载运行时,负载电流最小又能正常运行即可。
3.3 弹簧的设计
在弹簧螺杆式张紧装置中,弹簧的设计非常重要,刚性太大或太小均起不到应有的调节作用,因此,应正确选取技术参数进行设计。弹簧设计的总体要求是:应选择强力型压缩弹簧,簧径较粗,螺距较小,刚性较大,能承受较大的工作负荷,变形量不要求很大。由于输送机的工作性质不同,弹簧承受的载荷也不一样,所以对弹簧都需作针对性的专门设计,在确定主要设计参数后,再按机械设计手册中的设计方法进行计算和选择。主要设计参数包括:弹簧中径、最大和最小工作载荷、最大工作负荷时的变形量等。
弹簧中径应根据输送机尾部的结构尺寸、螺杆直径、牵引构件总张力的大小进行初选,通常取得较大,可为70~200mm,相应的簧径为6~25mm。
最大和最小工作载荷需具体计算,见图4。设有1水平输送的链式输送机,上部空载,下部承载。按牵引构件张力计算方法,可分为如图4所示的4个计算点,其中4点为最大张力点,1点为最小张力点,2、3点的张力与弹簧的选择有关。
T2=T1+W1-2································(4)
T3=CT2·····································(5)
式中
T1———1点的张力,N
T2———尾轮绕入点的张力,N
T3———尾轮绕出点的张力,N
W1-2———从1点到2点的运行阻力,N
C———张力增大系数,C=1.1~1.2
设牵引构件的初张力为T0,则有
Pmin=(T0+T2)/2····································(6)
Pmax=K(T0+T3)/2································(7)
式中
Pmin———每个弹簧的最小工作负荷,N
Pmax———每个弹簧的最大工作负荷,N
K———载荷不均匀系数,K=1.05~1.2
因张紧装置的弹簧是一侧一个对称布置的,故在式(6)、(7)中均除以2,考虑到载荷的不均匀性,在Pmax的计算中应乘以载荷不均匀系数K,也可理解为张力的变化系数。
最大工作负荷时的变形量也是一个要严格控制的参数,根据链式输送机的工作特性,此变形量不是很大,可根据表1所列的张紧行程值确定,通常为
Fmax=(0.05~0.10)S································(8)
式中 Fmax———最大工作负荷时的变形量,mm
有了以上设计参数,便可进行弹簧的计算和选择了。
3.4 防止紧固件受拉及壳体变形
在螺杆式张紧装置的结构设计中,应根据螺杆受压或受拉的不同情况,合理确定固定螺母件的位置,以确保由螺杆及尾部壳体受力,而不是由紧固件受力。下面以受压螺杆为例说明这一情况,见图5。
固定螺母2可放置在垂直侧板4的内侧或外侧,放在4的内侧时,螺杆1受压后,可将压力通过件2传到件4上,使壳体侧板受力,连接紧固件不受力;件2放在4的外侧时,螺杆1所受的压力则全由件2与件4之间的连接紧固件承受,当压力较大时,甚至会发生紧固件断裂的事故。所以,在受压螺杆中必须将固定螺母2置于壳体侧板4的内侧。对受拉螺杆同样存在这一问题,此时应将固定螺母置于壳体侧板的外侧。
有时虽然设计是正确的,但在生产制造中,工人未按图纸安装,常将固定螺母的位置弄错(因放在外侧安装方便些)。当螺杆受力不是太大时,位置装错还不会出大问题,若受力很大,出问题的可能性随之增大,由此导致的连接螺栓拉断的情况时有发生。因此,在生产、制造和检验中,要严格检查,发现错误应及时纠正。
当负荷很大时,壳体垂直侧板可能发生变形,此时可增加2块筋板3,防止壳体变形。筋板可事先焊上去,也可在发生变形后补焊,只是需将变形后的壳体校正后再行焊接。
3.5 尽量实现同步调节
当螺杆受压时,螺杆端头与尾部端盖板相对,与尾部相接的加料段把2侧的螺杆隔开了,此时调节不太方便,必须一侧一侧地进行,2侧调节量不一致时,会使尾轮歪斜,造成偏载,严重时还可能导致相关零件的损坏。因此,在结构允许的情况下,主张更多地采用螺杆受拉的张紧调节方式,此时螺杆端头与尾部端盖板在同一方向,只要使杆头伸出端盖板之外,便可十分方便地在2侧螺杆的端头各装上1个链轮,通过链条连接起来,实现同步调节,无论拧动哪侧的螺杆,均可使2根螺杆同时前后移动,这样就可避免上述弊端。
在采用受压螺杆的情况下,设计者可考虑把与尾部相接的加料段做成分离槽体形式,采用2侧加料,物料从侧面进入下槽体,这样便可利用上、下槽体之间的空隙,给螺杆端头配置与上述相同的链轮与链条,实现同步调节,见图6。在无法设计分离槽体时,还可考虑在2侧螺杆处配备刻度尺,用来指示每侧调节量。也可在每次调节后进行测量,看2边的调节量是否大致相同。只是这样做起来比较麻烦,还是同步调节最方便,也最安全可靠。
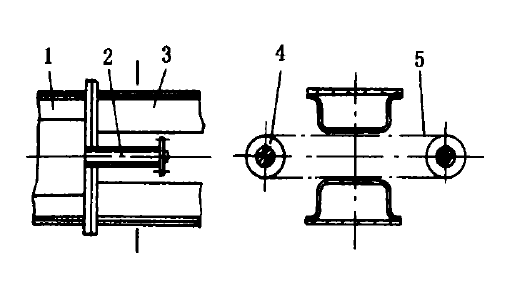
3.6 张紧行程的合理使用
在安装调试和使用中,要注意张紧行程的合理使用问题,否则,张紧行程可能不够用。
安装时,应先将螺杆旋出,让尾轮处在张紧行程的起始端,然后装入牵引构件,链条全部装入后,调节张紧装置,使链条适度张紧并获得初张力,输送机可以正常工作,此时检查张紧行程的使用量,应使已使用的行程不大于全部行程的一半,可用公式表示为
S1≤S/2····························(9)
式中
S1———首次张紧已使用的行程量,mm
S———张紧行程总值,mm
这样才能保证在今后的工作中,有足够的张紧量可用。如果首次张紧时使用的行程量超过了上述规定,则应重新恢复到原始状态,将链条卸下1节(模锻和双板链)或1对(套筒滚子链),再进行安装调整,便可达到要求。
3.7 小车重锤式张紧装置设计要求
以上介绍的设计要点都是针对螺杆式或弹簧螺杆式张紧装置而言的,小车重锤式张紧装置的设计与之有较大的区别,其主要要求是:
(1)尽量或优先选用地上式。
(2)张紧行程要加大,一般可比表1所列数值大2~3倍,如t=200mm时,S=315mm,而对于小车重锤式,S应为630~945mm,可取S=800mm。
(3)小车运行的导轨可采用轻轨,其长度应保证尾部在导轨上可运行的距离大于S。
(4)重锤离地不要太高,在500~1000mm之间为宜,以确保安全。如重锤位于人行通道中,应考虑安全措施。
(5)重锤的重量及数量根据计算确定,单个重锤可按100kg、50kg、25kg3种规格制造,要求外形一致,长、宽(或直径)相同,仅厚度不同,使安装和拆卸方便。
(6)若必须采用地下式,则应在地坑内考虑通风降温、防水防尘、照明及排水等措施,并应留出清理和检修空间。
(7)张紧行程合理利用的要求及调整方法与前述相同。
下一篇:提高螺旋输送机能力的途径
- 山东生物科技4000吨醇解木质素项目 {dede:field name='pubdate' function='GetDateMk(@me)'/}
- 延化化工上煤系统(皮带机+破碎机+滚筒筛) {dede:field name='pubdate' function='GetDateMk(@me)'/}
- 湖南湘福建材链板输送机项目 {dede:field name='pubdate' function='GetDateMk(@me)'/}
- 福建糖业锅炉输渣系统 {dede:field name='pubdate' function='GetDateMk(@me)'/}
- 新疆维吾尔盐湖盐业定量螺旋输送机项目 {dede:field name='pubdate' function='GetDateMk(@me)'/}
- 斗式提升机物料打结引起故障如何解决 {dede:field name='pubdate' function='GetDateMk(@me)'/}
- 影响斗式提升机提升速度的因素 {dede:field name='pubdate' function='GetDateMk(@me)'/}
- 斗式提升机的工作流程有哪些特点 {dede:field name='pubdate' function='GetDateMk(@me)'/}
- 如何提高提升机的运行维护水平 {dede:field name='pubdate' function='GetDateMk(@me)'/}
- 斗式提升机材质如何选择 {dede:field name='pubdate' function='GetDateMk(@me)'/}